Researchers at Stanford University in the United States recently released a new technology that promises extract lithium — a key component of electric car batteries — from highly saline lake brines at a cost 40 percent lower than the current dominant method. This could lower the market price of the mineral by as much as 75 percent.
According to the study published in Matter magazinethe new strategy for extracting lithium, called “redox couple electrodialysis (RCE)”, would offer greater reliability and sustainability in terms of the use of water, chemicals and land than traditional processes, which are called “slow, expensive and environmentally unsustainable”.
RCE is a type of electrodialysis a technique originally used in the treatment and desalination of seawater. It was only in the early 2000s that this electrochemical process of removing dissolved ions from a solution began to be used in the extraction of lithium from brines, until then done through solar evaporation and chemical precipitation.
What the Stanford team came up with was a change in the way the electrodes in the chemical cell that apply electricity to the brine work. Instead of two half-cell electrochemical reactions, they used just one on both electrodes. In other words, the hydrogen produced on one side is consumed on the other, creating a continuous cycle. and self-sustainable .
The challenges of lithium
A critical component in the transition to a green economy, lithium has quickly become one of the most sought-after elements on the planet. A 2022 report by consulting firm McKinsey & Co. predicts demand for the alkali metal will increase from 500,000 metric tons of lithium carbonate equivalent in 2021 to between three and four million metric tons by 2030.
While the lithium industry is expected to be able to supply enough product to supply the growing lithium-ion battery industry, there are concerns that the main sources of supply for the metal, salt lake brines and high-grade ores, may have some limitations on expected production.
Today, most of the world’s lithium still comes from rocks, mainly from deposits of spodumene, a lithium-containing silicate mineral found primarily in Australia. The other significant source of the alkali metal is dry lake brines found in the Lithium Triangle region of South America (Chile, Argentina and Bolivia).
However, whatever the prospecting method, its adaptability is limited. In the first case, due to dependence on the specific geological characteristics of each mining site. In the case of lithium extraction from brines, the current natural evaporation process depends on some climatic factors, such as abundant sunlight and low humidity.
The advantages of the new RCE technology
In a press release, study co-author Ge Zhang acknowledges that techniques for directly extracting lithium from brines have been in development for several years, but all of them face some drawbacks, such as “the inability to operate continuously, high energy costs, or relatively low efficiency.” He concludes: “Our method appears to have none of these drawbacks.”
To prove this, the study provides a brief technical-economic analysis that compares the current costs of extracting lithium with those of CER technology. In principle, significant savings come from eliminating the need for large-scale solar evaporation ponds, which are difficult to build and expensive to maintain. The reduction in financial costs includes savings in electricity, water and chemicals, not to mention sustainability.
By avoiding the extensive land use and water consumption of traditional methods, the RCE approach also reduces environmental impact of lithium production.
See: Event at Nasdaq shows advances in the Lithium Valley in MG
Furthermore, the new method also proved to be more “eclectic”, working with different types of saline water, including those resulting from oil production. Even the extraction of lithium from seawater, currently unfeasible using traditional approaches due to its low concentrations of the element, could be used, although this was not demonstrated in the current study.
RCE Scalability and the Future of Lithium
The authors expect their CER approach to cost between $3,500 and $4,400, equivalent to $20,000 to $25,000 per ton of high-purity lithium hydroxide, which can be easily converted into lithium carbonate, the preferred source of high-performance lithium-ion batteries for electric vehicles. Current production costs for extracting lithium from brine are $9,100 (R$51,400) per ton.
The current price of lithium carbonate is around $15,000 (R$85,000), after reaching $80,000 in late 2022. To serve this highly volatile market, the scalability of the RCE approach has shown promise in experiments. Even with a four-fold increase in scale, the new technology has proven productive energy efficient and with high lithium selectivity.
In fact, the technology tested two versions: one with faster lithium extraction and higher electricity consumption, and another slower one with lower consumption. However, the slower extraction delivered, in addition to lower costs, a more stable membrane to extract lithium uninterruptedly and for a longer time than the faster extraction.
They are continuing to conduct further tests, including with other promising membrane materials. According to the paper’s first author, Rong Xu, “As our research continues, we believe our method may soon be able to moving from the laboratory to large-scale industrial applications ”.
Meet the robotic fish that collects DNA from the bottom of the ocean
This content was originally published in New technique promises more sustainable and cheaper lithium extraction on the CNN Brasil website.
Source: CNN Brasil
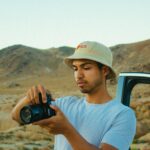
Charles Grill is a tech-savvy writer with over 3 years of experience in the field. He writes on a variety of technology-related topics and has a strong focus on the latest advancements in the industry. He is connected with several online news websites and is currently contributing to a technology-focused platform.